About me
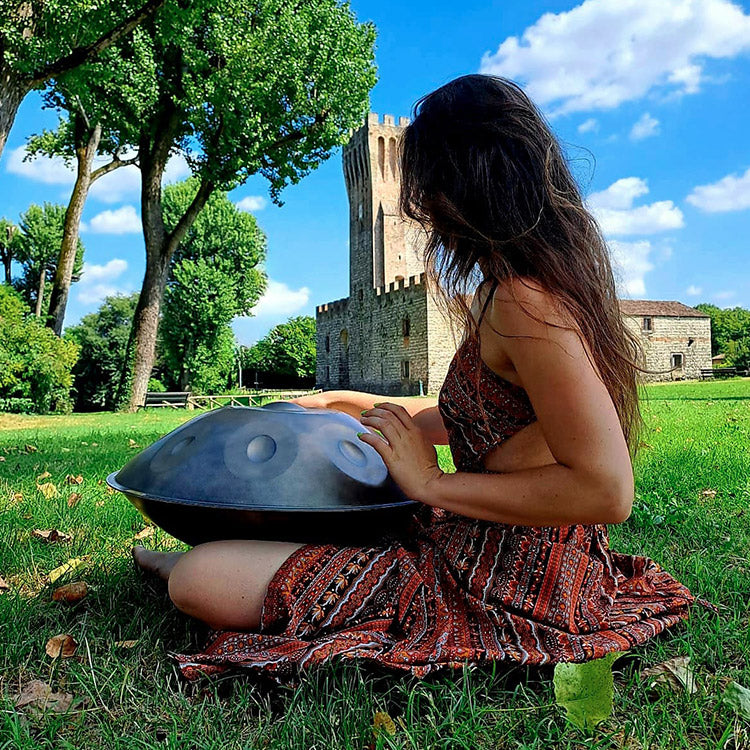
My story
I started building these wonderful handpan instruments in 2002 because a few months before I was fascinated by a musician who played this wonderful instrument, and obviously I wanted to buy one right away!
But..haime'..after in-depth research, I became aware of the great difficulty of being able to own one due to the problem linked to the very low production
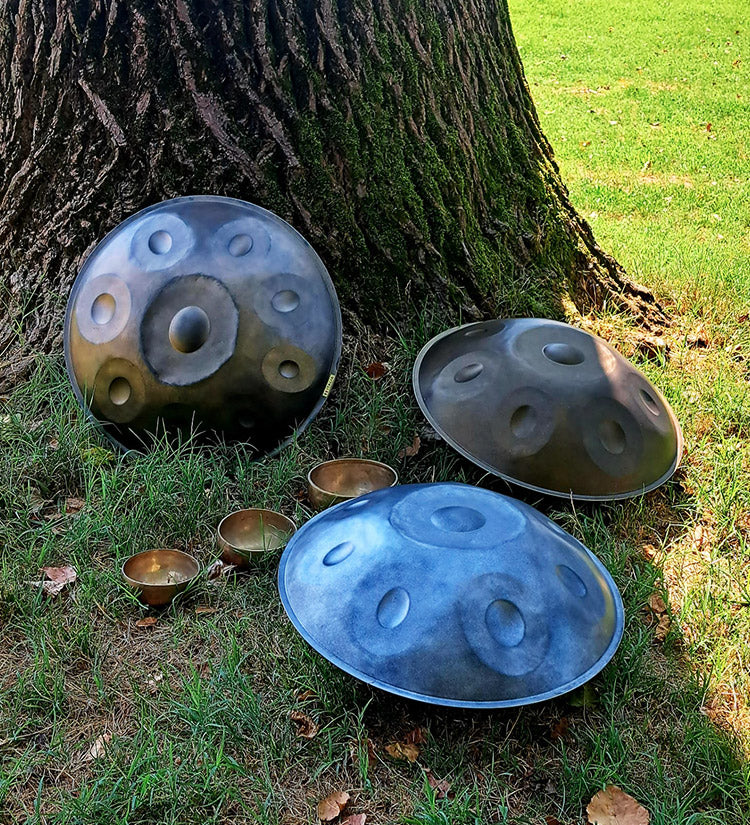
The reason for this poor production is due to the difficulty of the various processes for the manufacturers themselves in the creation of this instrument and, more importantly and predominant, is the impossibility of being able to build it at an industrial level. There are thousands of variables that change from instrument to instrument as it is built and only human intervention can manage these variables and make the right decision to make the instrument come to life.
In 2002 there It was impossible to own one of these magnificent instruments given the endless waiting list. However, in case you managed to get on one of the few waiting lists of that very small handful of artisan builders that existed worldwide, the waiting times involved years.
So I decided to build myself for me a Handpan with my own hands, given that I have always been a very practical person and trained and predisposed both in the field of music on a technical and instrumental level and for challenges.
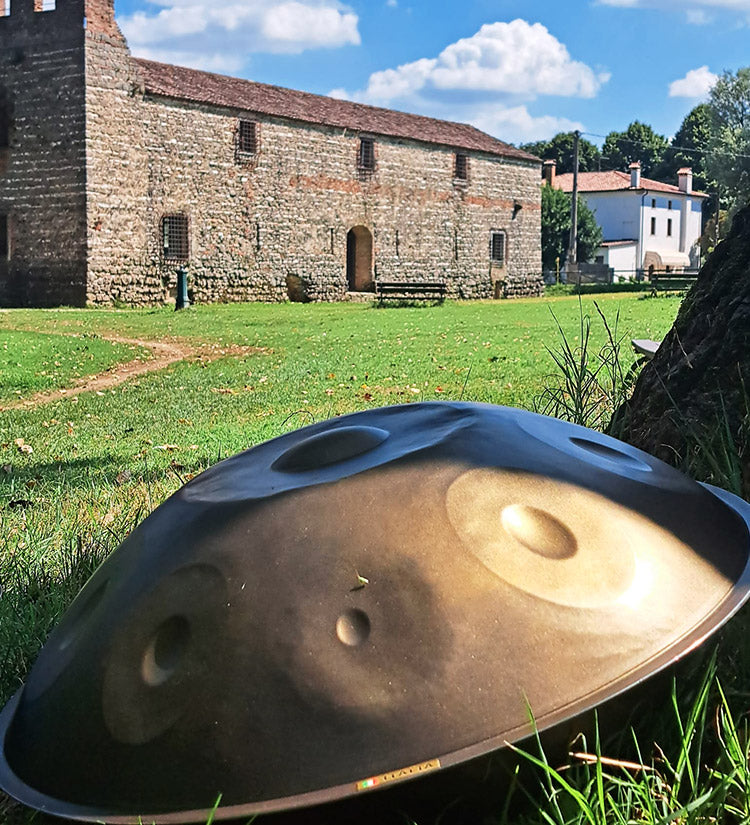
I have always been in the field of music in the electroacoustics sector and therefore what concerns Ohm's law and Helmholtz's law (law of resonance) has always been my field.
I was selected for my skills as a designer and sound engineer by famous brands in the music and audio sector and I have collaborated with famous world-leading companies in the electroacoustics sector designing audio systems and hi-fi transducers, winning many competitions in Italy, Europe and around the world, and in 2002 I received an honorable mentionfrom the Italian federation hi-fifor my self-built projects.
So, after all this curriculum on a technical level, I was very confident in being able to learn the secrets that this instrument hid. But, alas, then over time I realized that it was much more difficult than I thought!

This metal is thermally treated with a process called "gas nitriding": it is a heat treatment that has to do with quantum physics. The metal is placed in an environment from which the atmosphere is removed, the temperature is then brought to approximately 550°, then this environment is saturated with an anhydrous gas. When everything is ready, the iron nitrides are introduced, which, through the gas that the nitrides use as a vehicle, proceed with force on the metal and then stick into the grains of the metal, going deeper at about 1 cent per hour, thus changing the structure of the iron atom (the treatment lasts on average 10 hours).
From here is born the true and unique (very important to specify) ORIGINAL material with which these magnificent instruments are built, which according to TRUE PURISTS is the material that gives the warmest and most harmonious sound without interference.
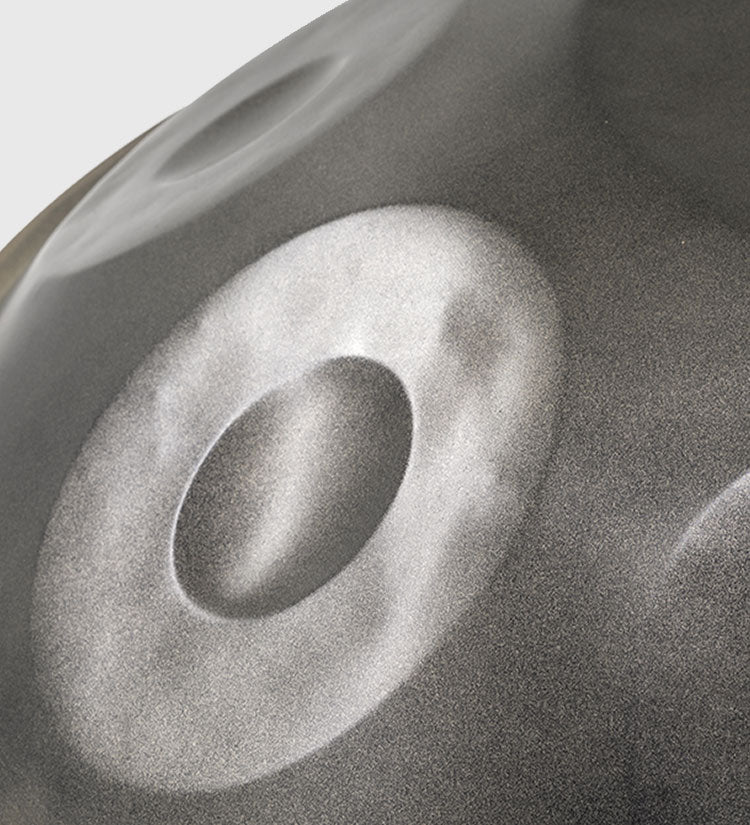
After the nitriding treatment, the actual creation of the instrument begins
- creation of the note fields, dimples/dimples
- formation and sinking of the intersectional part also called shaping
- note-by-note tuning with fundamental note, eighth harmonic and fifth harmonic
- gluing upper shell with lower GU shell (elastic polymer glue)
- 4 day rest
- first precision tuning (fine tuning)
- 2 day rest
- second precision tuning (fine tuning)
- second precision tuning (fine tuning)
- li>
- rest 2 days
- third precision tuning (fine tuning)
- rest 2 days
...and this until the instrument does not prove to be stable and good-sounding, on average after a period of a few months.
Many people in recent years have asked me how to build a Handpan or if I taught them to build Handpans: I always answer and I think deeply that this is an art that is impossible to teach there are basic information available to everyone on geometries and so on (known field shape, on the long axes there are the harmonic octaves, short fifth harmonic axes, etc...), but to be able to bring it to life is a completely different story, it takes experience and thousands of random hammerings to learn this art.
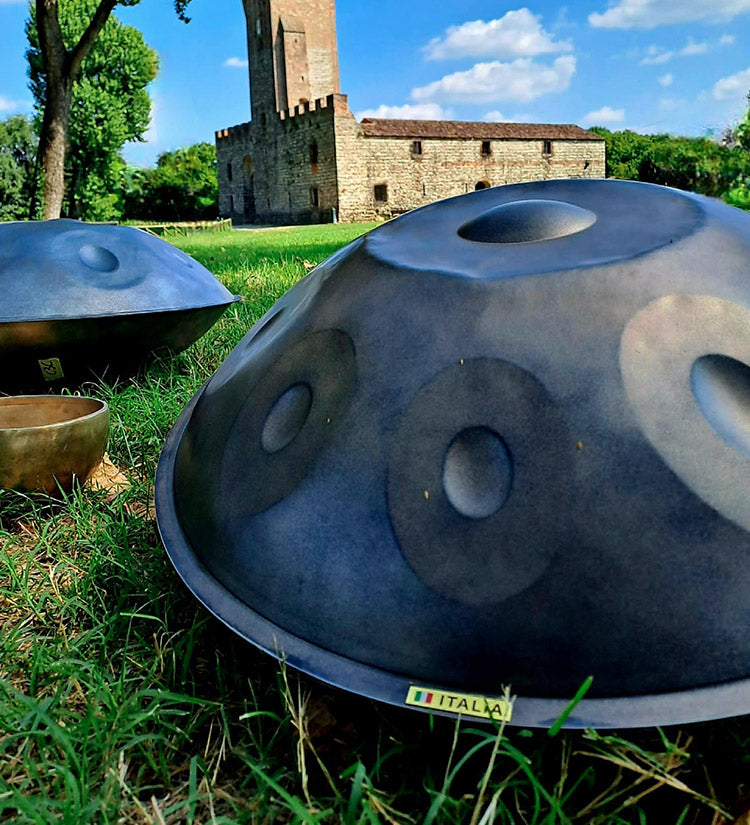
These tools are built with thousands of hammer blows, hammers of various sizes and of various materials and shapes. To create a Handpan, many thousands of hammer blows are needed and even the smallest dent positioned on the note field or in the intersecting part or in any area of the instrument serves to give balance to the whole instrument and make it magical.
Each instrument is different from each other (even if of the same musical scale): they always have a different production time and difficulty and also the positions of the hammer blows are always in completely different points.
This is another of the magic of this instrument: each instrument is unique, and to come to life it is essential to hand/mind/awareness of a human life and not of a machine.